Matching feed water pump designs with advances in gas-fired power plants
As the global demand for electrical energy continues to grow, more power plants are being built and their designs have to accommodate the changing requirements of the power generation market. Gas turbine manufacturers have developed larger and more efficient units, which need to be supported by advanced feed water pumps (FWP) to ensure long-term reliability as well as cost-effectiveness.
Patrick Welz – Head of Tendering EMEA for Sulzer, looks at how operators and manufacturers can work together to optimize performance and reliability.
Over the last 20 years, an increasing amount of energy has been delivered by wind and solar installations. These renewable sources produce power intermittently which means more traditional facilities, such as combined cycle power stations, now need to have the ability to make up the remaining output to match demand.
At the same time, the size of gas turbines has also increased with the advent of the H-class, which can be installed in combined cycle power plants to deliver up to 1’600 MW. Designing and building these installations is a major undertaking, which requires considerable planning and engineering expertise to ensure a cost-effective and reliable project.
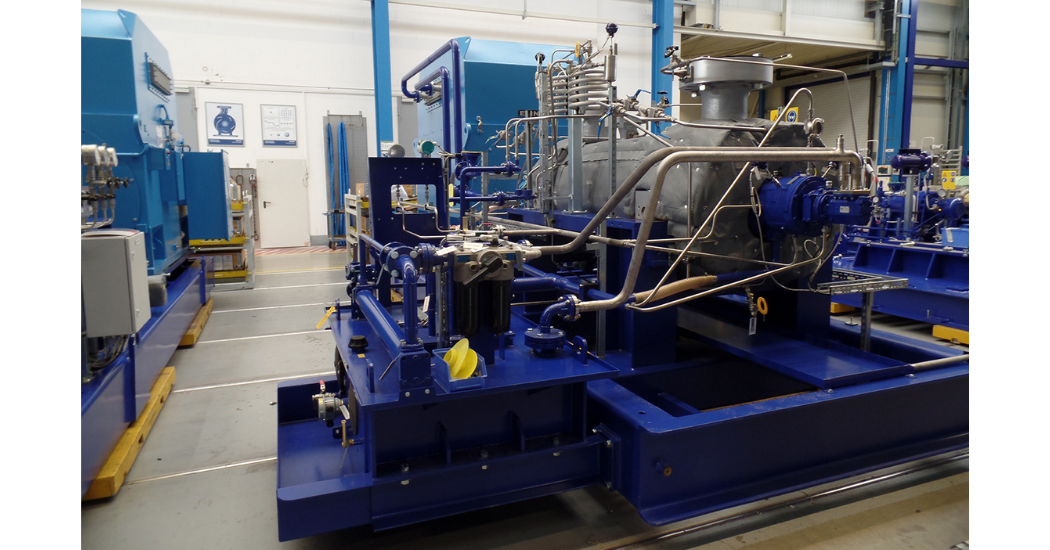
Feedwater pump in Sulzer workshop
Meeting demand
H-class gas turbines have been developed by the four major manufacturers of this equipment to meet the expected growth in demand worldwide. This has been combined with the greater generation capacity from renewable sources, to provide a more robust distribution network. In addition, the existing technology of the smaller combined cycle plants is continuing to be installed.
As a result, many gas turbines no longer run continuously, they are brought online as and when demand requires. This can mean several stop-start cycles every day, which can introduce new challenges for all of the equipment in the power plant.
During the initial design phase of the H-class turbine, manufacturers realized the sheer scale of the output, as well as the varying demand, would require design changes in some of the other equipment. They took the opportunity to work with pump manufacturers such as Sulzer on developing optimized pumps in tandem with the work on the turbines. In this way, when the new H-class turbine was ready to be launched, there was also a complete suite of pumps and other equipment that matched the performance demands and could be installed as a complete power generation solution.
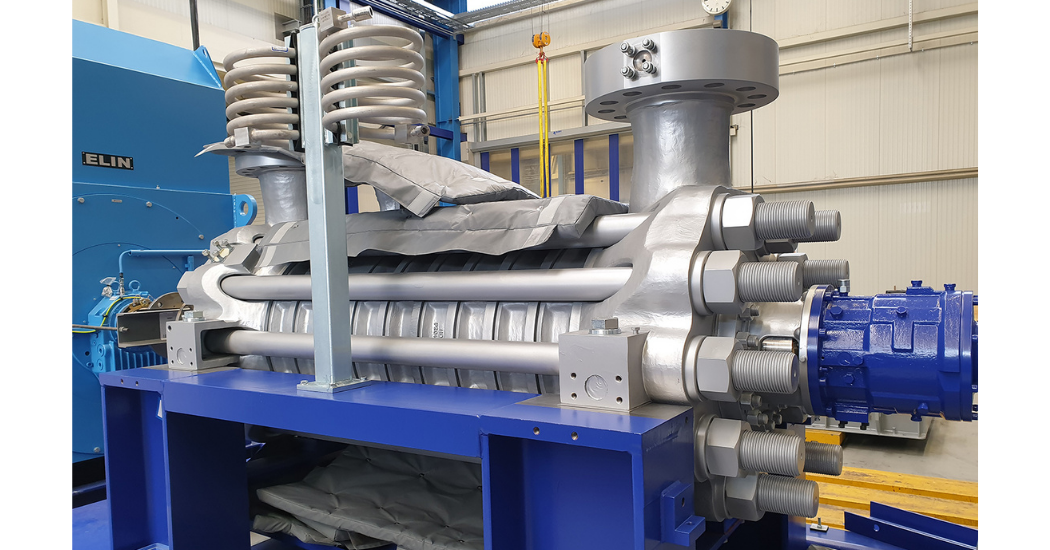
Feedwater pump without insulation
Case study: Flexible, efficient operation
In terms of size, the feed water pumps head the field and are specified to match the configuration of the power plant. In a 1-on-1 solution, where one gas turbine is operated with one steam turbine, there would typically be two FWPs in a duty/standby arrangement. In a 2-on-1 arrangement, there would be three FWPs with two of them operating under normal conditions and one on standby.
One of the most recent installations involving an H-class gas turbine was at Keadby 2, UK, where the 840 MW power plant is one of the most efficient in the world. To achieve its class-leading levels of performance, the plant uses a host of advanced technologies, and the UK energy company SSE Thermal partnered with major technology providers from across the world to design and build the power plant.
While Siemens Energy was designing the new gas turbine that was to be used in the facility, Sulzer was enhancing its product range to match the increased performance requirements of this equipment. In fact, through close cooperation with major gas turbine manufacturers, Sulzer engineered the first-in-class MD feed water pump, which has been installed in Keadby 2, to accommodate the varying conditions of operation and improve the overall efficiency.
The power station utilizes a 1-on-1 solution and Sulzer’s feed water pump configuration was selected as the best suited for the application. One of the design highlights is the hydraulic thrust balancing system, which includes a balance drum and thrust bearing that have been developed for long life under extreme operating conditions. The bearings as well as the lubrication system are also optimized for this application and the complete system is unaffected by rapid temperature variations associated with frequent start-stop operations.
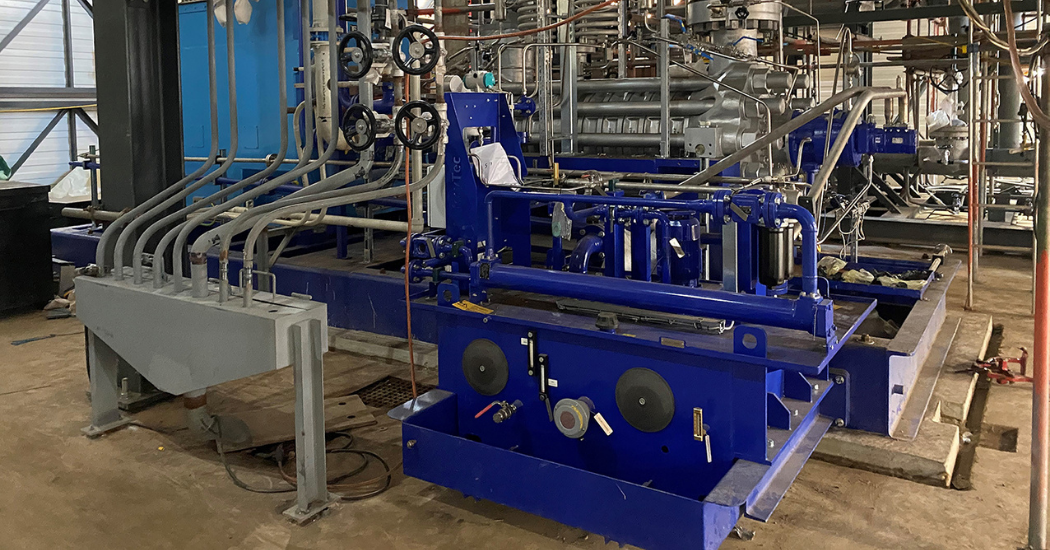
Site installation of feedwater pump
Building for the future
The process of designing and constructing new combined cycle plants is lengthy and complex; engineering procurement and construction (EPC) contracts cover the major design aspects with an aim to deliver the project to a budget. When it comes to the numerous pumps involved, the EPC will ensure the new equipment will meet the specifications for the project.
Very often, in projects of this scale, more than one EPC will be involved, with each being given responsibility for a certain part of the project. However, this can mean those responsible for the feed water pumps have no interaction with the team working on other assets. By bringing down this barrier, an expert pump manufacturer, such as Sulzer, can offer a more streamlined solution, including other main pump services like the condensate extraction and the cooling water pumps along with some other auxiliary pumps, with procurement and logistical savings for the project.
In addition, there is often little consideration for the long-term performance of the pumps and their overall life cycle costs (LCC). For the operator, proven reliability with the associated low maintenance costs and optimum efficiency are key factors for the cost-effectiveness of the plant.
Optimized performance
In addition to supporting the world-leading efficiency figures, the MD pumps also contribute to the goal of minimized maintenance. The operators of Keadby 2 for example have engaged in a 15-year long-term service contract, the first of its kind for an HL-class gas turbine in Europe. The design features of Sulzer’s pumps offer industry-leading availability with a robust construction and very low maintenance requirements.
For the plant operator, performance and reliability are very important, and this applies to all of the assets on the site. Selecting a manufacturer that can deliver a range of products to meet the specifications and quality requirements of the project, can have significant advantages in simplifying routine maintenance and spare parts.
Furthermore, when key suppliers have collaborated in the design of their products, their compatibility is assured and the integration with the wider plant is simplified. For the latest generation of gas turbine, operators can be assured the supporting pump infrastructure has been optimized and fully tested for this application.
Coordinated approach
By working more closely with a manufacturer that has the design expertise to deliver complete pumping solutions, significant benefits can be gained. Involving the pump manufacturer in the design of the infrastructure around pump assets for example can ensure enhanced pump performance while minimizing the footprint and cost of the structure.
Every gas fired power station, regardless of the size of the turbine, can benefit from the design expertise available from a pump manufacturer that is experienced in the power generation sector. By working more closely together, EPCs can achieve performance and budget targets while operators can take delivery of an optimized system that provides long-term reliability and efficiency.
About Sulzer:
Sulzer is a global leader in fluid engineering. We specialize in pumping, agitation, mixing, separation and application technologies for fluids of all types. Our customers benefit from our commitment to innovation, performance and quality and from our responsive network of 180 world-class production facilities and service centers across the globe. Sulzer has been headquartered in Winterthur, Switzerland, since 1834. In 2020, our 15’000 employees delivered revenues of CHF 3.3 billion. Our shares are traded on the SIX Swiss Exchange (SIX: SUN).www.sulzer.com. Our shares are traded on the SIX Swiss Exchange (SIX: SUN). www.sulzer.com. The Pumps Equipment division specializes in pumping solutions specifically engineered for the processes of our customers. We provide pumps, agitators, compressors, grinders and screens developed through intensive research and development in fluid dynamics and advanced materials. We are a market leader in pumping solutions for water, oil and gas, power, chemicals and most industrial segments.
Comments