The Forward Flow Project, instigated by Anglian Water, looks at the flows in a station or between a network of pumping stations and was developed to include a management tool that would improve the availability and efficiency of the pumping stations. The result is being seen as a step-change in pumping station control, reducing both operational and maintenance costs as well as improving flow management for the collection network as well as for the wastewater treatment plants.
The management teams responsible for wastewater treatment plants and the pumping stations that supply them, have two major concerns: dealing with the incoming flow of wastewater and ensuring that all the pumping stations in the local network are operating effectively. If either of these objectives are missed, the result could be a pollution incident which can carry significant financial penalties from the Environment Agency.
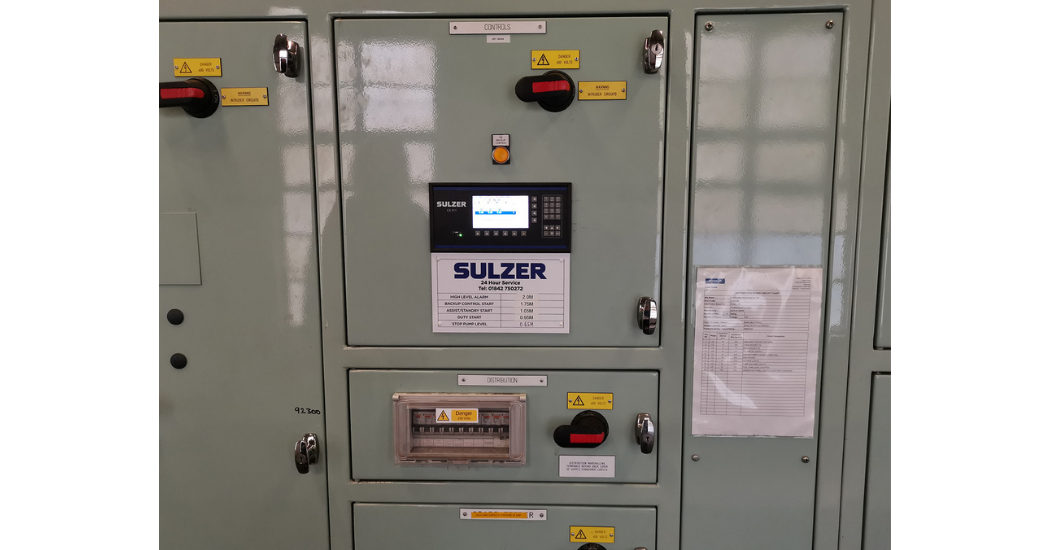
Sulzer’s HMI offers easy local setup and operation
Improved flow management
Anglian Water had identified the fact that it could make improvements to the visualization of wastewater building up in the system and the volumes expected to arrive at its treatment works. In addition, making individual pump capacity and efficiency data available to a central control point in near-real time would enable maintenance assets to be used far more effectively.
A discussion with Sulzer highlighted a possible solution that could not only provide flow data from every single pumping station but also a control aspect that could deliver more efficient pump control as well as improved pump management. This had the potential to mitigate the risk of flooding and maximize regulatory compliance as well as saving energy and reducing operating costs.
One of the major issues with pumping stations, and there are thousands of them, is dealing with pumps that have stopped working, usually because they have become blocked with debris. The most common alert for this is when the pump controls trip and an alarm signal is sent to the control room. On the smallest stations, this situation would leave one pump to deal with the inflow of wastewater until an engineer arrives to unblock and reset the other pump.
This task of unblocking pumps is both expensive and unrelenting. In the most simple cases, the pump can be operated in reverse briefly, the blockage cleared and then returned to service. When this action is not effective, the pump has to be lifted out of the well and cleared by hand. This requires lifting equipment, safety barriers and a considerable amount of time, all of which contributes to the operating expense of the wastewater system.
Sulzer’s pump monitoring system offers near-real time visualization of potential issues such as reduced flow rates or high current readings. These can be used to automatically initiate interventions such as reverse running or starting a mixer unit. This preemptive action greatly reduces the number of incidents that require engineers to be sent to site, cutting maintenance costs and improving reliability as well as saving energy due to increased efficiency.
Reduced pipe bursts
Another issue is pipe bursts, which are a major cause for concern for every water authority. The ageing infrastructure is susceptible to fractures caused by water hammer that is instigated by valves opening and closing quickly. The time and resources needed to reinstate the pipework are considerable, not to mention the inconvenience of having to divert flows around the damaged section while the repairs are completed.
By introducing improved pump start/stop procedures, it is possible to ramp flows up and down which reduces the tendency for non-return valves (NRVs) to close suddenly. This has gone on to reduce the frequency of burst pipes and made a significant reduction in maintenance costs.
Anglian Water has a long-term plan to improve the management of its wastewater network and use pump efficiency data to develop a proactive maintenance program. The first step was to assess the necessary technology and evaluate its effectiveness in meeting the project targets.
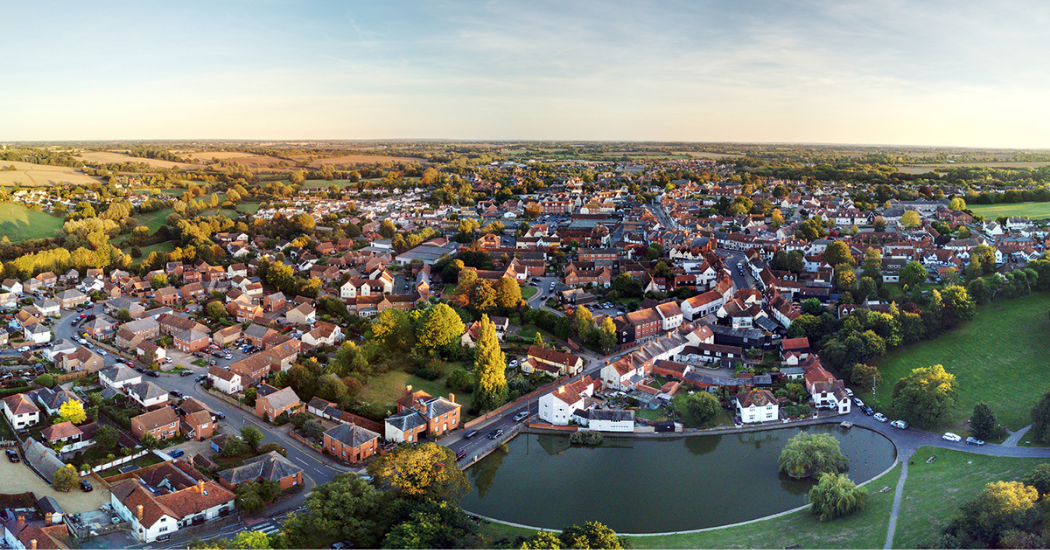
The Forward Flow Project has reduced both operational and maintenance costs for Anglian Water across the trial area
Improved technology
Jorgen Jager, Business Development Manager, Control & Monitoring, Sulzer Digital Solutions explains: “Our expertise in pump technology led us to offer the PC 441, which is a modular pump control system that works with the installed equipment. The additional functionality provides improved communications and additional sensor inputs.
The first trial pumping station was equipped with a PC 441, a submersible pressure sensor and a 3G modem, all of which were connected to monitor the station using an existing PLC, ultrasonic level controller and the station telemetry. Although the two pumps in the station were of an identical specification, one of the first observations was that pump 2 was developing a significantly lower flowrate than pump 1.
In addition, when a forced 2-pump pump-down was initiated, the pumps ran dry because the existing level detection system underperformed. In one event, the pumps ran dry for over four hours and to make matters worse, the telemetry system did not raise an alarm due to the station configuration.
Improved setup procedures
Sulzer’s data collection and visualizations highlighted this issue, as well as the difference in performance between the pumps. The original flow calculations involved manual set-points for the low pump capacity but the trial with the PC 441 offered an auto tuning sequence that is used to calculate pump capacity three to five times. In conjunction with the EC 531, a pump control and monitoring unit, Sulzer set up two setpoints that highlight the need for regular maintenance and emergency call outs.
The trial also used a pressure monitor of the outflow pipe that enabled the outflow calculations to be made with a more simplified setup procedure. When such a system is installed on a network of pumping stations, it is able to combine the data to produce accurate inflow figures for a treatment works using near-real time data.
This system has proven to be very valuable in identifying issues within pumping stations. For example, during the commissioning of a newly refurbished station equipped with two new, identical pumps, one unit showed a 20% lower capacity than the other. It was discovered that one of the pumps was not properly seated on the pedestal, allowing leakage between the pedestal and the flange. Once corrected, both pumps showed the same capacity. Without such a system, this kind of issue can go unnoticed for a considerable period.
Automated pump cleaning
Sulzer’s pump controller offers much more flexible control protocols that can optimize the operation of each station. Individual pump start and stop levels with adjustable delays or time-based pumping that reduce energy costs or provide a more even flow to the treatment plant. Pump cleaning cycles can be triggered by increased motor current, low pump capacity or as a regular event; this can have a major impact on the performance of a pumping station and reduce the number of visits required by maintenance engineers.
This system also offers the option of adding an energy monitoring unit, which allows the pump efficiency to be calculated and relayed back to the central control point. As the major cost for any water treatment company, having the ability to monitor and reduce energy consumption is a significant benefit.
Following a successful trial period where many of the benefits of the Sulzer control package were demonstrated, Anglian Water has begun a roll-out of the technology across its network of sewage pumping stations. The project also involves ABB and Vega Controls, which provide the variable frequency drives (VFDs) and radar-based level sensors and pressure sensors respectively.
The ongoing success of the project, known as ‘Near Real Time Modelling’ has seen it nominated for a Pump Center award and it went on to win the Wastewater Innovation Project of the Year 2019 honour.
Comments