Advances in additive manufacturing materials reduce repair times and extend turbine service life
Rotating equipment, such as gas or steam turbines and compressors play an important role in modern industry. The operators’ investment is usually recovered by long and reliable operation, but in some cases, due to their long service lives, the original equipment manufacturer (OEM) may no longer offer the necessary support. Continuous advancements in maintenance engineering mean that today, specialist solutions can quickly deliver reverse engineered, precision parts that benefit from modern materials and improved reliability.
Dr. Yogiraj Pardhi, Global Lead for Additive Manufacturing for Sulzer, looks at the latest additive manufacturing technique being used to create parts for legacy equipment.
Keeping legacy equipment in peak operational condition is very important to ensuring that productivity is maintained. Regular, planned maintenance is essential, but beyond that, there is a need to have a plan of action when more significant repairs are required. Fortunately, engineering technology continues to advance quickly and there are now solutions available even for high-specification parts, such as gas turbine airfoils.
Integrating modern components
Gas turbines are often used for driving larger pumps and compressors. Those manufactured in the 1960s and 1970s use legacy materials and technology, such as fabricated nozzles, which are made from several individual parts. Today, the modern equivalents are made from cast components that have properties to deliver improved reliability.
However, with the older machines now having little to no support from the OEMs, operators of these machines are looking for replacement parts from new sources. In this way, the equipment can be repaired cost-effectively and parts inventories can be updated by introducing modern materials in the replacement components.
Cost-effective support
Taking the gas turbine airfoils as an example, new parts for these machines are typically made using a casting process. This inherently requires a considerable amount of time to develop and qualify the finished product and the cost is affected by the volume of parts required.
Today, repair specialists, such as Sulzer, are looking to use the latest available technology to create new components cost-effectively, even in small quantities.
Additive manufacturing (AM) is a process that is supporting many industries, but qualifying new materials and achieving the necessary quality standards is a complex procedure requiring the highest levels of technical expertise.
Trusted expertise
In a recent project, a gas pipeline operator was looking to update a turbine that was powering a gas compressor. It needed two stator rings, each containing 42 airfoils. The operator has a long-standing relationship with Sulzer going back over 30 years, so it was natural that the first call for this project would go to the company that also delivered many repair solutions for the compressors and the gas turbines in the past.
Sulzer proposed a cost-effective solution within short lead time that also met the very high quality standards that are required in this application. Accelerating the pace of product development and manufacturing is a key advantage of additive manufacturing. With a great deal of experience in additive manufacturing for replacement parts, Sulzer recommended using this technique to make airfoils using cobalt-based superalloy Mar M 509™ material.
When made using selective laser melting (SLM), this material offers a number of benefits including high strength levels, good resistance to hot corrosion and excellent creep behavior at high temperatures. These attributes are paramount, since the stator ring airfoils will typically experience firing temperatures of 1,400 °F (760 °C).
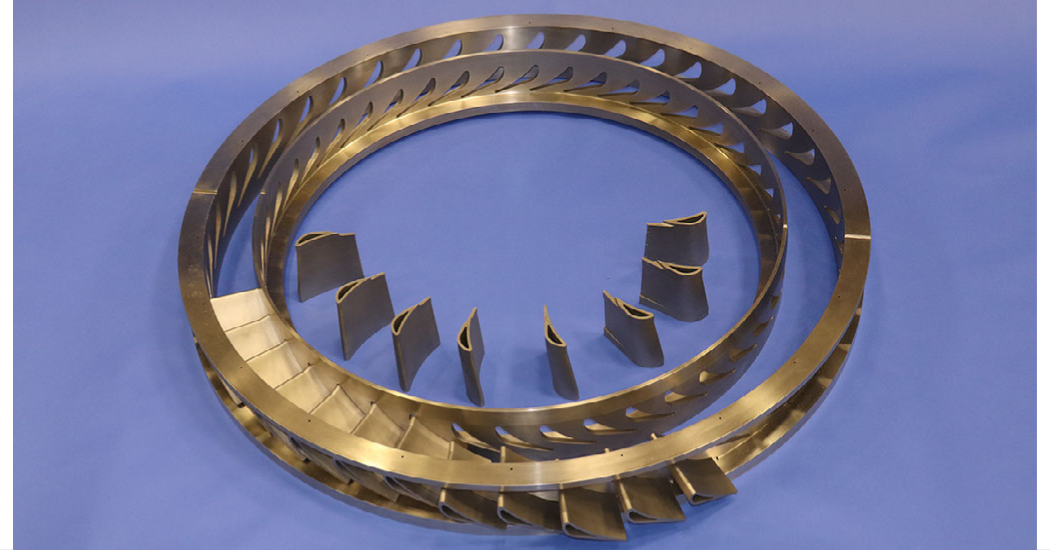
Additive manufacturing enables spare parts to be created more quickly and cost-effectively for small quantities
Qualifying new materials
Having established that the material is suitable, the next stage is to qualify the components. This involves in-depth trials and first article inspection work to perfect the manufacture of this component. Additive manufacturing for advanced engineering applications such as this requires each material to be properly tested and qualified before it can be approved for use in an AM design.
One of the biggest challenges was refining the manufacturing process to fit the properties of the material, in this case, Mar M 509. Sulzer used selective laser melting, which takes metallic powder and melts it in thousands of 2D layers with a laser before rapidly cooling it to create the component from a 3D model. The fast cooling process during SLM requires careful management of residual stresses by selection of a suitable laser scanning strategy.
Selective laser melting of complex superalloys like Mar M 509 is a technological feat that has only been achieved by a few. Sulzer is able to apply many years of experience in working with complex hot gas path superalloys to develop and qualify process parameters for this material.
The resulting process is very accurate and the final dimensions can be attained without requiring additional machining. The surface finish, internal and external, is achieved through careful selection of proprietary finishing techniques. The final properties of SLM material are achieved using an optimum heat treatment routine that was defined using extensive investigation into the effects of heat treatment parameters on material properties. After establishing the required SLM process and post processing routine, and on completion of First Article Inspection, the first set of 42 airfoils were delivered within eight weeks.
Precision engineering
In many cases like this, no original drawings are available, so, the designs for the new components need to be created using Sulzer’s in-house reverse engineering process. In this particular example, Sulzer created the new airfoils using a parent material which would withstand the high operating temperatures. On top of this, an additional thermal barrier coating was applied.
The final dimensions are established by the accuracy of the manufacturing process and from this point, the new airfoils are ready to be installed into the stator ring and welded in place. Post fabrication machining of the stator ring and application of the thermal barrier coating was completed in-house before reassembly into the gas turbine.
Long-term solutions
With successful qualification of the Mar M 509 material and fine-tuning of the manufacturing process, Sulzer can apply this solution to almost any industrial gas turbine that has reached a point in its service life where the OEM no longer provides support. Similarly, other components can also be produced using the same process.
Considering the age of these turbines, without replacement part support, the only alternative is to invest in a new gas turbine. In this case, the customer took the opportunity to replace the stator rings in two spare gas turbine with the same process, to further safeguard productivity.
Traditional methods of casting new parts for legacy machines requires a considerable investment in tooling. In contrast, while manufacturing costs are equivalent, SLM offers a substantial time saving and has none of the tooling costs. Operators of legacy machinery, which is still more than capable of delivering reliable service, can take advantage of modern maintenance engineering and enhance the supply of spare parts for the future.
About Sulzer
Sulzer is a global leader in fluid engineering. We specialize in pumping, agitation, mixing, separation and application technologies for fluids of all types. Our customers benefit from our commitment to innovation, performance and quality and from our responsive network of 180 world-class production facilities and service centers across the globe. Sulzer has been headquartered in Winterthur, Switzerland, since 1834. In 2020, our 15’000 employees delivered revenues of CHF 3.3 billion. Our shares are traded on the SIX Swiss Exchange (SIX: SUN). www.sulzer.com. The Pumps Equipment division specializes in pumping solutions specifically engineered for the processes of our customers. We provide pumps, agitators, compressors, grinders and screens developed through intensive research and development in fluid dynamics and advanced materials. We are a market leader in pumping solutions for water, oil and gas, power, chemicals and most industrial segments.
Throughout the Americas, Sulzer provides cutting-edge parts as well as maintenance and repair solutions for pumps, turbines, compressors, motors and generators. We service our own original equipment as well as third-party rotating equipment operated by our customers. Our technology-based solutions maximize reliability and lifecycle cost effectiveness.
For more information on Sulzer, visit www.sulzer.com
Comments