At-sea rewind restores performance and reliability for offshore vessel
Pumping crude oil ashore is a round-the-clock business that depends on onboard generators to provide vital electricity supplies. Removing a generator from service is a project that requires significant planning and technical expertise to ensure a cost-effective maintenance. For one oil and gas operator, that meant assigning Sulzer with the task of refurbishing one of its crucial assets.
The floating storage and offloading (FSO) vessel was built in 2003 and operates off the coast of Nigeria with a capacity of 2.2 million barrels of crude oil, which are pumped ashore via a 38 km (24 mile) pipeline. Operating in a particularly challenging environment, 15 years of continuous operation had taken their toll and the owners were planning some refurbishment projects, one of which related to an onboard generator.
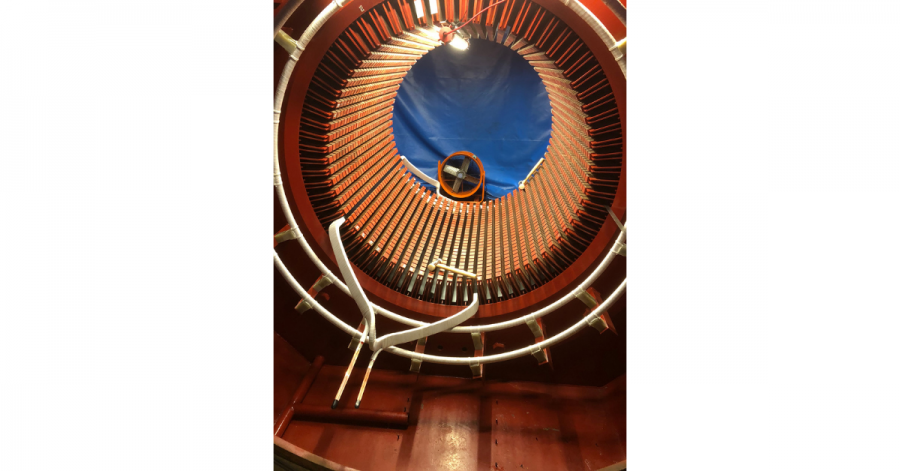
The first new coil in position as the rewind got underway
Detailed planning
During the course of operation, the 27 MW generator developed a stator winding fault that meant it could only operate at half of its design capacity. As such, the unit was assigned as a back-up generator until the stator could be rewound. The operators of the FSO began planning for this major overhaul and looking for a specialist company to complete the work.
With a service center in Port Harcourt, Nigeria, Sulzer was already very well-placed to deliver the maintenance project, especially considering its expertise in designing and manufacturing high voltage coils. Negotiations between the operator and Sulzer created a work scope involving experienced engineers from Birmingham, Aberdeen and the local service center.
In any project involving an offshore installation, all those working on the vessel or platform must be properly trained and certified to ensure their safety. Many of Sulzer’s engineers have completed the offshore safety induction and emergency training (BOSIET) course, which means they can be deployed without any delays. Furthermore, Sulzer’s staff and facilities are certified to work on machines that operate in potentially hazardous atmospheres, making them an ideal choice for offshore maintenance projects.
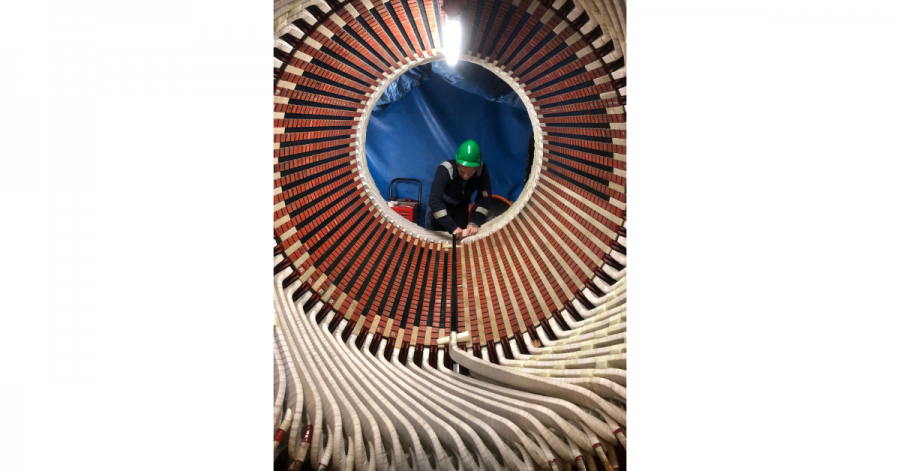
Applying the finishing touches to the stator rewind
Laying the groundwork
The initial site visit identified a number of challenges for repairing the generator. In order to gain access to the stator, some surrounding infrastructure needed to be dismantled before the rotor could be removed using a specially-made frame. A landing area was required to store the rotor and other components while the stator was being rewound.
Once the project was given the go-ahead, Sulzer began designing the framework that would be needed to remove the rotor safely and making arrangements with the FSO engineers to create a protective area around the stator. This served a dual purpose; it shielded the working environment around the stator and the additional dehumidifiers minimized the moisture content of the air, which can affect testing procedures.
Creating precision coils
While the generator was being dismantled, the new coils were being manufactured in Sulzer’s coil shop in Birmingham, UK. The design of the 72 new diamond coils used the latest Class F insulation technology, which consumes less space, allowing more room for additional copper, making the generator more efficient.
The new coils were precision-shaped to match the stator slot configuration of the generator. The shape of each coil was checked using a wooden template that exactly replicates the slot positions to ensure an easy installation process when they arrived on the vessel.
As part of the refurbishment, all electrical components were inspected and tested before being reassembled. The rotor, exciter, permanent magnetic generator, and auxiliaries were all checked and carefully stored as part of the project.
During the strip-down, the stator slots were cleaned before the electromagnetic core imperfection detection (ELCID) tests were carried out to ensure the laminated core was undamaged. Once the coils arrived from the UK, the engineers completed the rewind, adding the blocks and bracing to provide a solid installation.
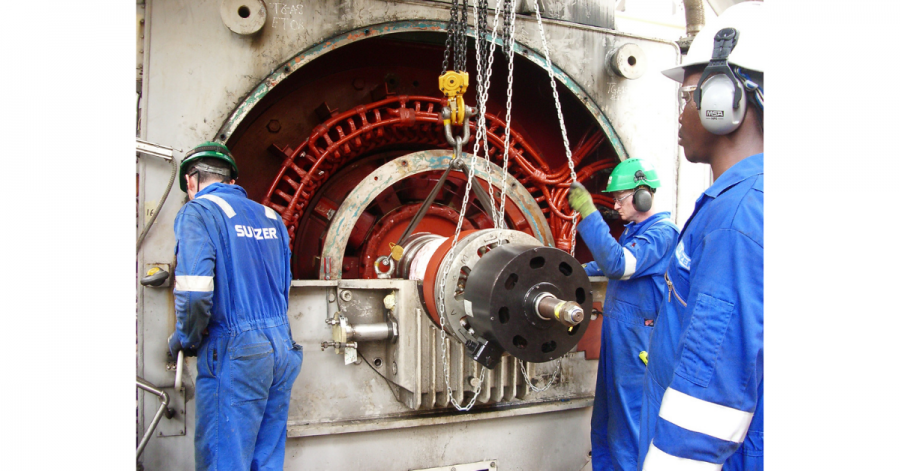
Reinstalling the rotor as the project draws to a close
Delivering performance
Once the rewind was complete, a further week was required to reassemble the generator, carry out testing and commissioning, before the unit could be returned to normal service. In this case, special procedures and knowledge had to be applied to the whole repair due to the generator being classified as a hazardous area machine
Tom Freestone, Head of Customer Support Services at Sulzer’s Birmingham Service Center, commented: “Working in an offshore environment is always a challenge, but our multi-skilled team has successfully delivered this project. We have drawn expertise from the local service center as well as from the UK to ensure the rewind was completed to the highest standard.”
About Sulzer
Sulzer is a global leader in fluid engineering. We specialize in pumping, agitation, mixing, separation and application technologies for fluids of all types. Our customers benefit from our commitment to innovation, performance and quality and from our responsive network of 180 world-class production facilities and service centers across the globe. Sulzer has been headquartered in Winterthur, Switzerland, since 1834. In 2019, our 16’500 employees delivered revenues of CHF 3.7 billion. Our shares are traded on the SIX Swiss Exchange (SIX: SUN).
Comments