A new pump system solves corrosion and viscosity problems from polyacrylamide use.
By: Rob Martindale, Watson-Marlow Fluid Technology Group
As part of the Little Traverse Bay Environmental Project in northern Michigan, environmental consulting firm Pescador LLC treats groundwater using a niche polymer. When their diaphragm metering pumps proved ineffective in handling this chemical, they worked with Watson-Marlow Fluid Technology Group to install a new low maintenance, high-accuracy pumping solution.
Polymer Use in Dewatering: Viscosity and Corrosion
Polyacrylamide (PAM) acts as a flocculant. As one of the steps utilized in Pescador’s process, this anionic polymer attracts huge numbers of the miniscule organic material, pin-flocs that float in the solution to concentrate them as a larger floc. Once gathered in this way, dissolved air floatation (DAF) can push the debris to the surface so it can be skimmed off.
However, PAM and other polymers challenge traditional off-the-shelf pumping systems. Using a diaphragm metering pump, equipment failure plagued Pescador with downtime and high costs. “We had constant maintenance challenges,” recounts Pescador Plant Manager Ryan Wcisel. “They were always clogging up; the dosing wasn’t very accurate—it was a struggle to keep the equipment running optimally.” The chemical attacks standard santoprene tubing, and with highly viscous polymers such as at this site, rapidly wrecks pumps that are not specifically designed for such a task.
In search of a lower maintenance solution, Pescador contacted Watson-Marlow Fluid Technology Group. Generally, when the customer encounters a problem because they are pumping a niche chemical, or needs more control, that is when they contact Watson-Marlow. Our experts suggested a new product, the Qdos ReNu PU.
The Qdos 20 ReNu PU pumphead installed at the site on the DAF application lasted over two years and never failed (application details: 0.015 USGPH, 24/7, 365) before being replaced due to minor calibration drift.
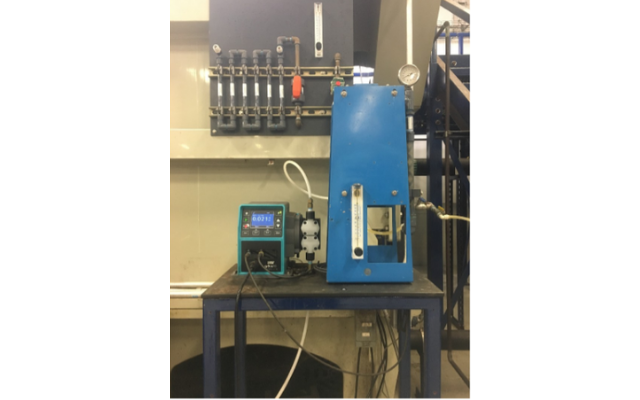
When pumping polymers, Watson-Marlow Fluid
Technology Group’s Qdos ReNu 20 PU pump outlasts other pumps by years.
Specialized Tubing for Polymers
At the heart of the solution is a new tube technology that increases the chemical compatibility range of Qdos. Specifically designed with polymers in mind, the tubing is aliphatic hydrocarbon resistant, so the chemical does not attack the tubing in the way it otherwise would. In addition to protecting the pumphead, the peristaltic pump protects the chemical itself. Polymers are susceptible to mechanical degradation. If agitated and mixed prior to use, the chemical will not work as intended. During the high-shear pumping process of a diaphragm pump, the pump’s moving parts come into contact with the polymer, damaging it and leading to clogs and seizures. As a peristaltic pump, the Qdos20 ReNu PU can pump polymer in a controlled and very low-shear movement without causing any degradation to or agitating the chemical. Through Watson-Marlow’s peristaltic technology, the pump protects the chemical Pescador is injecting in the process.
Now, Pescador uses four of the pumps, one on the DAF system and three on centrifuge units. Wcisel identifies three key benefits to the innovative pump: ease of use and maintenance, metering accuracy, and pump feedback.
The Qdos 20 ReNu PU pump is made up of two main components: the drive, which includes the pump’s intelligence, and a separate pumphead, which is the only consumable part of the pump. This makes the Qdos a drop-in solution, whereas diaphragm metering pumps need four or five ancillary systems (backpressure valves, pulsation dampeners, strainers, float switches)—each with their own maintenance schedules. For example, the check valves on Pescador’s original diaphragm metering pump set-up proved inadequate in the face of high viscosity. The Qdos pump also eliminated the need for flooded suction which the diaphragm metering pump depended on.
This consolidated system is also entirely enclosed, offering a major improvement for spill reduction. Polymer is a very slippery chemical. Any leak entails a lengthy and involved clean-up process, and attempts to clean up polymer with water expands the chemical and perpetuates the clean-up operation. With a diaphragm pump, this could easily consume one or two hours of clean-up time after a spillage. In the Qdos 20 ReNu PU system, the specialized tubing sits within the sealed housing (ReNu Technology) of the pumphead, so if a leak should develop, the pumphead contains all spillage. Especially valuable in cases of hazardous or expensive chemicals, this feature minimizes chemical waste. It also avoids the entire spillage remediation process; instead, users simply replace the pumphead—in about two minutes, and all without using tools.
Additionally, the Qdos 20 ReNu PU offers excellent metering precision. The pump delivers an accuracy of ±1% to limit chemical costs that would result from overdosing, improve process performance, and reduce bi-product transportation costs. Furthermore, when pumping polymer, the viscosity level of that chemical can change. The Qdos 20 ReNu PU is engineered to maintain a constant level of accurate metering against variable viscosity. “The accuracy of the dosing is unparalleled by anything else we’ve seen,” Wcisel says. Along with greater precision, the system’s new tubing technology also provides more flow.
Moreover, the pump’s smart notification system improves operational efficiency. When the tube ruptures or is at end of life, the Qdos 20 ReNu PU notifies the user. It also supports flexible batch process control, alerting an operator when a drum is almost empty. “One of the nicest features that we haven’t found on anything else is the feedback that we get from the pump— to get an alarm that alerts the user to change the pumphead,” says Wcisel. Along with an easy-to-use interface, this makes the pumps, he says, “very user friendly.”
Innovative Pump System Provides Uptime and Less Maintenance for Environmental Water Treatment
Water treatment facilities that use polymers in the dewatering process can limit costs and downtime by switching to a specialized pump with purpose-designed tubing technology. As polymer usage continues to grow internationally as a part of primary, biological, mixed, and digested sludge processing, polymer-specific pump systems will prove a critical technology for the next generation of environmental and industrial dewatering.
Comments